Why Aluminum Repairs Need Specialized Tools
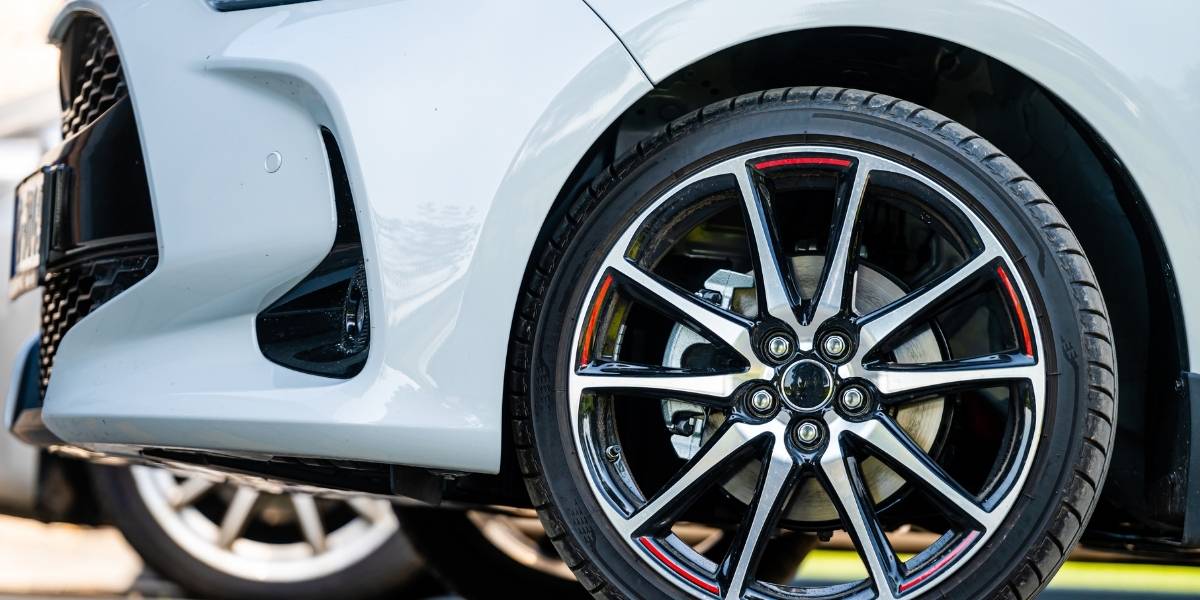
Aluminum is widely used in modern vehicles due to its lightweight and corrosion-resistant properties. While it offers significant advantages for fuel efficiency and performance, repairing aluminum body panels is far from straightforward. Unlike steel, aluminum reacts differently to stress, heat, and repair processes. Because of this, traditional auto body repair tools often fall short, making specialized equipment an absolute necessity.
Many auto repair shops invest in dedicated aluminum repair stations to prevent cross-contamination and ensure proper repairs. Without the right tools and techniques, an aluminum panel can weaken, affecting a vehicle’s safety and durability. If you’re looking for aluminum repair in Lorton, VA, it’s crucial to choose a facility that understands the unique challenges of working with this material.
1. Aluminum’s Unique Properties Demand Precision
Aluminum behaves very differently from steel, requiring specialized techniques for repairs. One of the key differences is its molecular structure, which makes it more prone to work hardening. This means that when aluminum is bent or reshaped, it becomes more brittle and less malleable.
Steel, on the other hand, has a “memory” that allows it to return to its original shape under the right conditions. Aluminum lacks this property, making repairs more challenging. Without the proper tools, attempting to reshape aluminum can lead to cracks or warping, compromising the vehicle’s structural integrity.
2. Preventing Cross-Contamination with Dedicated Equipment
Steel and aluminum do not mix well in an auto repair environment. When aluminum comes into contact with steel, a process called galvanic corrosion can occur. This leads to deterioration and weakens the metal over time.
To prevent this, professional repair shops use separate tools and workspaces dedicated exclusively to aluminum. Specialized aluminum repair stations are designed to keep aluminum dust and steel particles from contaminating each other, ensuring a clean and controlled environment for high-quality repairs.
3. Welding Aluminum Requires Advanced Equipment
Traditional welding techniques used for steel are not suitable for aluminum. Because aluminum dissipates heat much faster than steel, it requires different welding techniques to ensure strong bonds.
Shops that repair aluminum use high-frequency TIG (Tungsten Inert Gas) welders or MIG (Metal Inert Gas) welders with pulse technology. These tools provide the precise heat control needed to avoid overheating, which can weaken aluminum. Without these specialized welders, aluminum panels can easily become misshapen or structurally compromised.
4. Specialized Dent Repair Techniques
Standard dent repair methods, such as using a steel stud welder, do not work on aluminum. Because aluminum does not have the same memory as steel, traditional pulling and pushing methods are ineffective.
Instead, professional repair shops use specialized aluminum dent pullers and adhesive-based systems that apply controlled force without damaging the surrounding area. These tools allow technicians to reshape aluminum panels effectively while maintaining their strength and structure.
5. Heat Sensitivity Requires Controlled Repair Methods
Aluminum is highly sensitive to temperature changes, which means excessive heat can weaken its structure. Unlike steel, which can tolerate a wide range of temperatures, aluminum loses its strength quickly when exposed to high heat.
To address this, specialized heat induction tools are used to warm up aluminum in a controlled manner before reshaping. Without this step, excessive force can lead to cracks or permanent damage to the metal. The use of infrared thermometers and heat monitoring devices ensures that the aluminum is not exposed to temperatures that could compromise its durability.
6. Riveting and Bonding for Structural Integrity
Many modern vehicles with aluminum panels rely on rivets and adhesives instead of traditional welding. This method ensures a strong, lightweight bond that meets manufacturer safety standards.
Specialized rivet guns and structural adhesives are essential for these repairs. Using the wrong type of rivets or adhesives can weaken the vehicle’s crash protection, making it unsafe for the road. This is why manufacturers provide strict guidelines on the types of fasteners and bonding agents that must be used in aluminum repair processes.
Aluminum repair is not a task for just any body shop. It requires specialized tools, dedicated workspaces, and trained technicians who understand the unique challenges of working with this material. Whether it’s welding, dent repair, or bonding, using the wrong techniques can compromise a vehicle’s safety and performance.
If you need aluminum repair in Lorton, VA, trust Kolex Collision Center to handle your vehicle with expertise and precision. With dedicated aluminum repair facilities and specialized equipment, you can be confident that your car will be restored to its original strength and safety standards.